Not every type of stone is suitable for building a stove in a house or in a bath. The furnaces are subject to high temperature differences, which only special materials can withstand. In addition, the stove should not only give off heat, but also accumulate it - this will reduce fuel consumption and increase efficiency.
What materials are suitable for the construction of furnaces?
First of all, this:
- fireclay bricks;
- red refractory;
- heat-resistant alumina;
- clinker.
These materials are full-bodied, they do not deform from the heat, do not break - the stove from such materials will last for many years.
It is impossible to build furnaces from:
- hollow stones;
- silicate materials;
- slotted bricks.
The listed types of materials are not heat-resistant, they quickly deteriorate with frequent heating, deform, and do not hold heat.
Important: you can lay out the oven only from full-bodied stone! Hollow can not withstand large temperature loads.
Types of bricks for the furnace
Fireclay
Fireclay brick withstands up to one and a half thousand degrees Celsius! It is made of refractory clay with the addition of fireclay chips and aluminum oxide. Then it is fired in a special way according to a strict scheme.
Outwardly, the stone looks porous, the color faded red with a yellowish tint, dark spots are visible. By weight, it seems lighter than usual, despite the fact that there are no cavities in it. Due to the lightweight mass, fireclay brick masonry is quickly heated and conduct heat well.
Most often, fireclay is not used for the entire stove - they spread places that directly contribute to the fire. This is explained by the high cost of the material: chamotte is 5 times more expensive than ordinary classic stone.
Fireproof red
This type of stone is cheaper than fireclay, therefore, stoves from it are most often folded. Basis - refractory clay. The composition also includes coke and quartz powders, graphite chips.
Outwardly, it looks like a well-known classic brick, but solid, without cavities. The color is yellower than the classic. Suitable for laying out the outer lining of the stove, and those parts that come in contact with the fire.
The stone has a high heat capacity, that is, it is able to accumulate heat and then give it away for a long time. Such material can be used to put together a Russian stove, a barbecue stove or a bathhouse.
Alumina
The most popular material on the market in terms of price / quality ratio. It is fireproof, can withstand up to 1300 degrees Celsius. At the same time, it is durable, does not deform, is not afraid of sudden changes in temperature.
Furnaces in a bathhouse are often laid out of alumina bricks: the material is so strong that cold water can be poured onto heated bricks to create steam. In this case, the stove will be suitable for operation for many years.
Clinker
It is a heavy parallelepiped of dark color. The surface is flat, almost without pores.
You can choose such a stone for the construction of the furnace, but the construction will be very expensive. Due to the high cost in Russia, it is rarely used. In addition, the maximum allowable clinker heating temperature is 1300 degrees, which is slightly lower than that of fireclay.
Stamps
In addition to the variety of building materials, you need to pay attention to their brands. Key Features - This is a brand in terms of density and frost resistance.
Density Grade shows the strength of the material. If the stove is in a house or in a bath, a brick with a density grade of 200-250 will do. The indicator above is completely unnecessary, since then the kindling will take too much time.
Frost resistance you need to consider when building a chimney, as well as if you are building an outdoor barbecue stove. The frost resistance brand shows how a stone absorbs and gives off moisture. For pipes and street buildings, you need to choose the most frost-resistant brands.
The most common manufacturers
In Russia and in the neighboring countries, brick produces many factories. The following types are most common for masonry furnaces:
Borovichi. Produced at the factory of the same name in Nizhny Novgorod. High frost resistance, density 250.
"Vitebsk workshop". Produced in Belarus. Density of 200, but frost resistance is very low. They can lay stoves indoors, such a stone is not suitable for pipes.
"Fireclay". It is produced by various enterprises, for example, Belokamensky plant in Ukraine, Sukholozhsky plant in Perm. It is recommended to use in the construction of those parts of the furnace that directly touch the flame.
The choice of brick in appearance
When buying a brick, you need to pay attention not only to what density grade it has, how frost-hardy it is, but also how high-quality it is made. To do this, carefully inspect several stones from the party. The edges of the building materials should be flat, without potholes. At the stone of the Borovichi plant, the edges are somewhat rounded.
Measure the angles: they should be 90 degrees. Measure the length and width of the stone: a maximum difference of 1.5 - 2 millimeters from the dimensions declared by the manufacturer is allowed.
Ask the seller to show the cleaved stone to evaluate its internal structure. With a good material, the chip should be evenly painted over the entire surface. The uneven color of the cleavage, the presence of spots, indicate that the internal structure is not homogeneous, and therefore not equally strong.
Another test option: apply a slight blow with something metallic on the largest face of the stone (for example, a hammer). If the brick does not contain internal cracks, the hammer will bounce with a jingle. A dull sound from the impact indicates defective material.
You can drop a brick: high-quality crumble into several large parts, not high-quality - into small pieces.
Ask the seller to provide documentation on the compliance of the brick with GOSTs. GOSTs and their transcripts must be indicated in the papers. It should also be indicated that the brick is suitable for the construction of furnaces.
To summarize
So, which brick is better for the stove? To lay down a high-quality stove, you need to correctly approach the choice of brick. It should be:
- Corpulent.
- High Quality.
- Refractory.
- Density grade 200 - 250.
- Possess high frost resistance.
- Conform to GOST.
Last tip: always buy the number of bricks with a margin so that there is no situation when building materials are not enough. Buying a brick later is not recommended, since stones from different lots can differ in color and quality.
Watch the video: “Which brick to choose”
Fans of a steam bath in a Russian bathhouse are well aware that a brick stove and a metal stove are, as they say, two big differences. According to some lovers of light steam, these are generally two different philosophies and two different views on bathing matters.
Of course, modern compact metal stoves have many advantages. These include:
- small size;
- light weight that does not require a capital base;
- ease of installation even without experience.
But the brick kiln has its own advantages, which often outweigh the scales in favor of choosing a brick structure. Here are just the main ones:
- the brick oven perfectly retains heat;
- gives softer steam;
- the bath does not cool for a long time, being heated by the accumulated heat;
- more durable when using high-quality heat-resistant brick.
Brick stoves also have disadvantages, which include large dimensions compared to metal stoves, the longer time required for heating, as well as the need to involve a master stove-maker who knows how to fold the stove correctly so that it quickly heats up and cooled for a long time.
If these disadvantages are not significant for you and you want to have the softest steam and spend less fuel to maintain the desired temperature, then the choice is clear. However, before construction begins, you need to determine the material from which the furnace will be laid out.
Today in the market you can see many different offers with fairly attractive prices. But how can one not make a mistake and choose a brick for the stove, which will last a long time and provide the bath with soft heat?
We will talk about this in this article.
What brick can be used for the stove?
For different sections of the furnace, various requirements are imposed on the brick from which they are laid out.
In the furnace, maximum temperature stresses occur. Temperatures can reach 1200 ° C. The figure below shows graphs of the burning temperature of firewood at different relative humidity of the wood and various coefficients of excess air (α):
Not every brick can tolerate the effects of such heat without destruction. Therefore, for the device of the furnace space requires a brick with maximum heat resistance. As a rule, this is fireclay brick.
In cast-iron stoves, a significant part of the heat generated by burning wood is transferred to the steam room directly through the walls. In this case, the temperature of the exhaust gases turns out to be quite low - no more than 300-450 ° C.
Unlike cast-iron heaters, much less heat is transferred in the brick kiln through the walls of the furnace, due to the much lower thermal conductivity of the brick. Therefore, the temperature of the flue gases in it is much higher and reaches 800-900 ° C. As you understand, the design of the chimney in this case should have much higher heat resistance. Therefore, in brick stoves for the installation of gas ducts, heat-resistant ceramic corpulent brick is most often used.
Fireclay brick
Fireclay bricks are made of high-alumina refractory clay. Fireclay bricks are produced in accordance with GOST 8691-73 "General Refractory Products. Shape and Dimensions."
Brick size ША-5 and ШБ-5 is 65x114x230mm:
Brick size ША-8 and ШБ-8 is 65х124х250:
The main physico-chemical characteristics of ША-5 (8) and ШБ-5 (8) bricks are shown in the table below:
Name of indicator |
Norm for the brand |
|
Mass fraction,%: |
||
Al2O3 not less |
||
Refractoriness, ° С, not lower |
||
Additional linear shrinkage or growth,%, no more |
||
at temperature, ° С |
||
Open porosity,%, no more, for group products: |
||
The compressive strength, N / mm2, not less, for products of the subgroup: |
||
Softening start temperature, ° С, not lower |
The industry also produces fire-resistant fireclay bricks of the following types:
Mark |
The form |
Size mm |
Softening point, ° С |
straight one and a half |
|||
straight three-quarter |
|||
end wedge |
|||
end wedge |
|||
rib wedge |
|||
trapezoidal transverse |
65 / 114x190x230 |
Of all the grades produced, for the construction of stoves and fireplaces, ShA and ShB bricks are most often used. ShKU finds its application in the lining of steel casting ladles in the steel industry, and broadband access for lining the domain.
You can watch tips for choosing a brick for the furnace in this video:
Bricks produced by "LODE"
Refractory bricks manufactured by the Baltic company LODE are very popular for the construction of furnaces.
The table below shows the main characteristics of fireclay bricks LODE:
The company has a representative office in our country.
How to choose a refractory brick when buying?
In order not to run into a batch of low-quality bricks, it is best to buy it from large time-tested manufacturers, looking for recommendations and reviews on the Internet.
When inspecting a batch, be sure to pay attention to the same size by comparing several bricks. The deviation of the dimensions of the length / width of the products should be no more than 2 mm.
A visual inspection can help identify defective bricks. For example, large black spots indicate a non-compliance with the temperature regime during firing and indicate a burn.
Cracks are also not acceptable. Such a product will quickly crumble during operation.
Also, in the body of the bricks there should not be large lumps of unmixed clay or any foreign inclusions.
A good fire-resistant brick should have a uniform color, a uniform structure and, when tapped with a hammer, produce a sonorous sound, indicating a high density of the material and the absence of internal voids.
What bricks can not be used when laying the stove?
It is impossible to use a hollow red brick from ordinary clay, products from silicate materials and slotted bricks for the construction of a bathhouse furnace.
Due to the lack of the necessary physical properties, such a material will not be able to withstand thermal stresses and soon can simply collapse, turning into brick crumb.
In addition, it should be remembered that the laying of furnaces is also carried out on a special solution made of refractory clay and crumb brick. Normal masonry mortar is not allowed.
Brick masonry scheme
In order for the stove to quickly warm up and cool down for a long time, while keeping warm, you will need to find a specialist stove-maker who knows his job, or rummage through the forums on the Internet, in search of optimal orders.
But in general, the layout of the furnace masonry is as follows:
The numbers in the figure indicate: 1- foundation; 2 - waterproofing (roofing material); 3 - floor;
4 - brick base of the stove; 5 - firebox; 6 - chimneys; 7 - facing; 8 - overlap; 9 - pipe; 10 - roof slope; 11 - slide gate.
In the lower part, a foundation is laid that transfers the load from the weight of the stove to the ground. The foundation may be made of monolithic reinforced concrete or foundation blocks of suitable sizes, pre-treated with waterproofing to prevent corrosion of the material of which the foundation is made.
Most often, the top of the foundation is slightly below the level of the clean floor of the bath. A layer of roofing material is laid on top of the foundation and then 2-3 rows of strong brick, on which the furnace itself will stand. Brick for this site should be selected based on sufficient strength and resistance to freezing in the winter. Here you can use a slightly burnt fire-resistant brick (grade III).
As already mentioned above, the material from which the furnace space is laid out experiences the greatest thermal load. Here, temperatures reach 1100-1200 degrees Celsius. Only fireclay bricks can withstand such temperatures without destruction. In this case, only products of the first grade should be selected.
The main part of the furnace volume is occupied by flues of a rather complicated configuration, providing not only good draft, but also receiving the main part of the heat of the outgoing flue gases, accumulating in and then transferring this heat to the steam room. Since the temperature of the flue gases of a brick furnace does not exceed 900 ° C, a red corpulent ceramic heat-resistant brick is quite suitable for the installation of gas ducts.
For the installation of the chimney, brick should be selected based on resistance to temperature extremes. after all, during the furnace fire inside the smoke channel, the temperature can reach 300 ° C, and on the street at the same time there may be a cracking frost.
In order to prevent the pipe from collapsing due to such changes, it is most preferable to have a two-layer construction device, where the inner layer of the barrel is laid out from heat-resistant bricks, and the outer one - from bricks having the lowest density and the highest heat transfer resistance.
Facing brick for subsequent finishing can be II grade. Minor flaws will subsequently be hidden by plaster or tile.
Before proceeding with the masonry, experienced craftsmen sort the bricks, as different types of products may appear on one pallet.
How to calculate the required amount of brick?
In order to purchase the required amount of brick, you will need to make a calculation based on its size and dimensions of the stove.
Knowing the size of the brick of each type, from which a certain part of the furnace will be laid out, it is necessary to calculate the number of rows in height and width, adding an allowance for the thickness of the seams (about 10 mm) and a certain percentage for the fight and fit.
It is better to immediately get the right amount with a small margin than to buy material later if there is a shortage.
For the construction of heating stoves in individual residential buildings, ceramic bricks are widely used. The construction industry produces a wide range of bricks for masonry kilns, but which one to choose from the proposed range? Before we consider this issue, you need to understand the fact that two types of bricks are used for laying the furnace - it is a simple ceramic brick, but with certain characteristics, which is used for laying the external elements of the furnace, chimneys and fireproof or fireclay brick, which is used for masonry furnace furnaces.
What properties should have a brick used for laying a furnace
The kiln brick must meet the following technical requirements:
- Resistance to high temperatures and effects of an open flame.
- The ability to accumulate heat and keep it for a long time.
- Sufficient mechanical strength.
- Resistance to significant temperature fluctuations.
Solid fuel furnaces are built of ceramic bricks that meet the requirements of GOST 390-96. This standard came into force on July 1, 1997 and establishes the technical conditions that these products must comply with in shape and size. The regulatory document also defines the requirements for the use of products depending on the maximum ambient temperature.
For ceramic bricks intended for the construction of thermal units, more stringent requirements are applied than for other building materials. In the furnace of a furnace, the flame temperature can exceed 1000 ° C; accordingly, its walls are subjected to significant heat loads. Thermophysical parameters of the material used must be higher than the specified value.
During operation of the furnaces, they are regularly cooled in individual cases and to negative temperatures. Brick undergoes a significant difference in ambient temperature, which leads to thermal expansion with subsequent compression. The product must have a sufficient margin of safety in order to successfully resist this phenomenon and to avoid deformation and destruction.
The brick used for laying stoves must have a sufficiently high thermal conductivity and the ability to accumulate heat. The first property is necessary for the rapid heating of the room and the transfer of energy from the burnt fuel to the external environment. The second quality allows you to maintain this process after the cessation of combustion in the furnace for a long time. This allows you to maintain a comfortable thermal regime for a long time.
The use of different types of bricks for laying various elements of the furnace
Solid fuel furnaces have a rather complex design, the components of which work under certain conditions. The question arises, what kind of brick is needed for laying the furnace and its elements?
The device of the heating furnace is as follows:
1. Firebox and blew.
The combustion chamber mainly has two-layer walls, the inner one is made of refractory (fireclay) bricks, the outer one is made of facing ceramic bricks. The firebox is erected from fireclay bricks with maximum refractory properties. The external finish of the furnace works in less stressful conditions and it is possible to use facing bricks with excellent decorative characteristics.
2. Smoke channels.
Smoke channels are a large heat exchanger and the temperature in them, although lower than in the furnace, is still quite high. For laying these elements of the furnace, fireclay bricks are used. Outside, the structure can be faced with ceramic tiles or facing bricks.
3. Chimney.
The chimney is in direct contact with the atmosphere and experiences large temperature differences. Therefore, a ceramic brick with the highest possible frost resistance is used for it. Typically, this element also has a two-layer structure with a decorative exterior finish of ceramic brick or metal box.
The process of laying the furnace and an example of the use of fireclay bricks for building highly loaded elements and external cladding with ceramic bricks.
The use of bricks with the appropriate characteristics for the device of individual elements of the furnace will provide maximum durability and excellent thermophysical properties. Experienced stove makers in the selection of material pay special attention to this issue. At the same time, a thorough inspection and rejection of bricks with large cracks and deep damage and chips is performed.
What characteristics should have ceramic brick for laying the furnace and fireclay brick for laying the furnace
Characteristics of ceramic bricks for laying external elements of the furnace, smoke channels and pipes
As we said earlier, a certain type of ceramic brick is used for laying the stove; now we will consider what basic characteristics this brick should have.
Brand by density. The first thing you need to look at when choosing a ceramic brick for an oven is the density grade. The brand of ceramic brick in density is set in accordance with the requirements of GOST 530-2012. For its designation, an alphanumeric coding is used, consisting of the letter “M” and a number from 25 to 1000. Please note that this indicator does not indicate the quality of the brick, but only shows its density when pressed. This indicator is important because the denser the brick, the slower it heats up, and therefore cools more slowly. The fact that the brick will slowly cool is certainly good, because the stove will give off heat for a longer time. But it’s more difficult to heat a stove made of too dense bricks, especially when it has completely cooled down. Balance is important here, therefore, brick is used for masonry with a density not lower than M-150 and not higher than M-250.
Frost resistance. Frost resistance of a product is defined as the ability to withstand a certain number of heating and cooling cycles. This indicator is indicated by the Latin letter F with the addition of a number from 25 to 300. The frost resistance index of ceramic bricks is important in the construction of external elements of a heating furnace, such as chimneys. The thing is that this integral part of the furnace is in very severe conditions of constant temperature difference. This has a huge effect on the brick used for laying the pipe. For the construction of such structures, it is best to use ceramic bricks with frost resistance from F75 to F100.
Thermal conductivity. The thermal conductivity of ceramic bricks will depend on its density and for products used for masonry, it should be in the range from 0.59 to 0.72 W / (m × ° C).
Fullness. For laying the furnace, only full-bodied ceramic bricks are used.
Ceramic stove brick.
For laying the combustion chamber of furnaces, fireclay brick is used with the following characteristics
- Product brand: ShAK, PB, ShA, ShB, PV, ShV and ShUS.
- Softening point not lower than 1300 ° C.
- Uniformity of blocks throughout the volume.
- High density and low porosity of products.
The operational characteristics of the furnace and the duration of its intended use directly depends on the quality of the refractory bricks of which the furnace is built.
The building materials market offers an extensive range of products suitable for masonry fireboxes. The question arises from which brick it is better to lay the stove so that it is durable and retains its properties for a long time. Experts recommend the use of fireclay chamotte semi-acid brick. These products have the best ratio of characteristics in terms of cost and thermophysical properties and quality.
The main technical characteristics of ceramic bricks used for the construction of solid fuel furnaces are summarized in the table:
Fireclay brick.
Choosing a kiln brick manufacturer
The market for this type of building materials is extremely saturated with products of domestic and foreign companies. Products manufactured by enterprises from Russia, Belarus and the Baltic republics are widely represented in this segment.
Vitebsk brick factory workshop number 1.
Ceramic bricks of this manufacturer meet the requirements for material for furnaces according to the density brand. Frost resistance of products is extremely low. The density grade is 180 - 200. Brick can be used for facing the stove and chimney channels, it is unsuitable for other elements. We can say that this is one of the most common, to date, materials for the construction of the furnace. It can not be used for laying the furnace and the first chimney of the furnace. It is required to make the lining of the furnace and the first chimney with refractory fireclay bricks.
With constant direct contact with fire, this brick is quickly destroyed. Since the products have low frost resistance, the use of this brick for laying the outer walls of the chimney street pipe is also excluded. The advantages of this material include the fact that this is one of the most budget options and given all the nuances to use it for laying the furnace is quite possible. Has 2 working surfaces. In general, the quality of this brick can be described as satisfactory.
Brick brand LODE is made in the Baltic states. Ceramic brick has a high mark in density - 500 and frost resistance. The product is used for facing the outer surfaces of the furnace and chimney. Brick of this brand has various forms and it is often used to create all kinds of decorative elements of the furnace. In its main purpose it is a facing brick.
Borovichi brick factory.
Products of Borovichi brick factory located in the Novgorod region. Mass production began in 2011, experts evaluate its quality as good. Density grade of ceramic brick M-250, frost resistance at F25. Significant deviations of products from the sizes established by standards, up to 10 - 12 mm in one batch, are noted. This must be taken into account when laying the furnace and it is best to take a little more brick than necessary. Further, everything depends on the professionalism of the stove-maker and his ability to select the necessary products. The brick has rounded upper and lower edges and 3 work surfaces.
Refractory or fireclay brick of Russian production.
The quality of the products varies greatly, from frank marriage to decent products. Fireclay brick has an even cream color and high density, the shape is regular with right angles. As we found out earlier, this brick is necessary for lining the combustion chamber of classic stoves, hearths and fireplaces. But it’s rather difficult to single out certain manufacturers here.
The answer to the question which brick is best for the furnace is usually decided by the customer in agreement with the master. It takes into account several factors, among which the main ones are compliance with the requirements of standards and cost. The operational properties of the structure depend on the correct choice of refractory bricks; saving to the detriment of quality is expensive.
Methods for determining the quality of stove bricks
Verification of compliance of this type of building materials with the requirements of regulatory documents is carried out according to the methods approved by the Gost series. Each of them is designed to determine the individual characteristics of refractory bricks:
- GOST 5402.1-2000. Method for determining residual deformations after heating.
- GOST 4069-69. The method of monitoring the fire resistance of products.
- GOST 151136-78. Methods for measuring damage to corners and edges of ceramic blocks.
Brick research is carried out in laboratories using special equipment. At home, it is impossible to check the quality of refractory bricks using the methods described in the standards. The buyer has to rely on the certificates and qualifications of the master, whom it is desirable to involve in deciding on the choice of material for the construction of the furnace.
Experienced stove makers are able in many cases to determine the quality of refractory bricks according to some criteria. Furnaces are built only from solid ceramic bricks with a brand from M150 to M250. In this case, the certificate must contain a note stating that the specified product is intended for this type of work.
The following methods are used to determine the properties of bricks:
Vibration and sound. On a large facet of the brick, which is kept on weight, a weak blow is applied with a hammer. The tool should bounce off the surface with a jingle. This indicates the absence of internal cracks.
If you are planning to build a stove with your own hands, then the key material that you must use to build it is brick. And how to choose a brick for the furnace among the huge assortment of this material, this is the problem. After all, the wrong material can very quickly destroy a built furnace or provoke an unpleasant event, for example, a fire or something else. We offer you an article on the right choice of bricks for laying a furnace.
Types of bricks depending on the material
So, before choosing this or that material as an oven masonry, you need to understand what its varieties exist depending on certain characteristics. So it will be more clear which brick products can be used in the construction of the furnace.
According to the material, bricks are divided into two types:
- ceramic;
- silicate.
The first is made by firing methods based on clay mixtures, and the second consists of a mixture of sand and lime, as well as impurities. Such material is made in an autoclave, and if one or another pigment is added to the mixture, it will acquire the desired shade.
- ordinary solid brick - it is used for internal masonry;
- front or finishing - such bricks are needed to finish the finished masonry of a finished building. Unlike the first, it has a more uniform structure, looks more neat and has smooth edges.
Varieties of Ceramic Bricks
When masonry is used, ceramic products are used, and they, in turn, are divided into three grades, each of which is perfect for laying one or another part of the furnace:
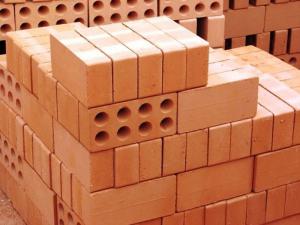
The use of products of different grades in masonry
When masonry use materials of all three grades, depending on its part. So, during the construction of the furnace, they are required for the construction of such elements as:
- foundation;
- firebox;
- smoke exhaust;
- facing works;
- smokestack.
Since the foundation is the supporting structure of the furnace structure, it should be as durable. At the same time, it is impossible for it to damp from below; for this, the material must have a water-repellent property and be frost-resistant. In order to build a foundation, products of either the first or third grade are needed, the reasons for this choice are as follows:

Remember that inside the furnace the temperature is able to rise above 1100 degrees, and ceramics are not always able to withstand this. Therefore, for its construction take other types of products - refractory, in particular, fireclay.
Types of Refractory Bricks
The most common types are chamotte and quartz.
Chamotte products are made by pressing and firing at high temperatures. For the manufacture of furnaces are used fireclay materials and sometimes quartz for individual parts of the furnace.
Quartz bricks are made of their quartz sand, for laying the furnace such sand is used only in places of interfacing with load-bearing structures made of metal, for example, beams or pallets. But it is forbidden to use it in the body of the furnace, since they should not react with substances that have an alkaline reaction. And in the construction of the foundation of the furnace can use lime.
Fireclay bricks are not so finicky in terms of pairing with other substances. If the solution is prepared properly, it will serve reliably when used for laying the furnace.
What technical characteristics of a brick should be taken into account when working
To build a furnace with your own hands, of course, you need a refractory brick. But that is far from all. Here is a list of characteristics that need to be considered when choosing a brick for the furnace:
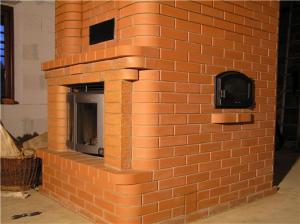
For the construction of the furnace, choose solid products without voids from the inside, as well as products that have a basic single size (model). It is highly undesirable for bricks of different modules to be used during the construction of one furnace, since in this case it will be difficult to dress the seams and the furnace will not be durable. Another module can only be used for the construction of a furnace furnace.
What bricks can not be used
In no case do not use the following types of products for the construction of a stove with your own hands:
- raw
- silicate;
- brick made by slip casting.
Raw can become sour even in a damp room when the oven is operating, the second model does not differ in heat resistance, and the third can simply crumble from constant thermal shocks. Also hollow products cannot be used, with the exception of individual cases.
Also, if you decide to build a stove in your country house, for example, for a bath, do not neglect the advice of friends who already have relevant experience. They will tell you which brick to choose for work, so that it lasts as long as possible and did not cause any problems.
The stove is laid out of brick of a special composition. It must be refractory, refractory, properly burned. It is not necessary to take one of its appearance. If you know which brick to use for the stove in a certain part of it, you can save on expensive material without loss of quality. For example, the firebox should be laid with fireclay bricks, for the body and chimney, you can take a standard refractory, and make the outer clinker or special cladding. This option is more economical than the entire construction of fireclay.
Fireclay brick: properties, sizes
The best material for laying the stove is fireclay brick. Its characteristics are unrivaled among refractory materials:
- withstand t \u003d 1500ºC,
- characterized by a low degree of hygroscopicity,
- large temperature differences do not affect the integrity of the structure.
Chamotte for masonry is made from refractory clay mixed with chamotte powder. Its quantitative composition is 70%. Manufacturing requires the observance of the smallest details: burnout will make it glassy, \u200b\u200band burnout will cause more moisture absorption. Standard sizes of fireclay bricks:
- 250x124x65 mm
- 230x114x65 mm
- 230x114x55 mm.
The color is yellow-beige with a splash of red or brown. The composition is regulated by GOST 390-96. Fireclay bricks are denoted by the abbreviation SHA or SHB. This material is necessarily fulfilled. In metal furnaces it is used for lining the firebox.
How to put fireclay?
It should be noted that it is not enough to know from which brick the stove is laid, it is also important to understand the types of mortar for it. For example, fireclay brick requires the use of masonry mix with a similar composition. It means that the solution should contain chamotte in the same ratio. This masonry provides the same reaction of materials to heating and cooling, since they have the same expansion coefficient. This ensures the strength, reliability, durability of the thermal unit.
Refractory brick
Furnace refractory brick is used for the construction of the body and chimney channels, if the number of fireclay is limited. It is made of red refractory clay with the addition of quartz sand. Withstands temperatures up to 1000ºC, has a high heat capacity, fire resistance, strength. It yields only to fireclay in physical properties. Not intended for masonry in places where there will be contact of the surface with an open flame.
Standard sizes:
- 250x120x65 mm,
- 250x85x65 mm.
With this material, you can cover a metal chimney above and below the roof. Also, a brick chimney is being built from it alone. Available in red and brown shades. For masonry, a mixture of a similar composition is used. It is also required to ensure uniform expansion and contraction under thermal loads. It is better to use the ready-made mixture that the brick manufacturer offers.
Masonry Features
Fireclay and standard furnace materials always have a homogeneous solid structure without cracks and voids. They allow you to reduce the thickness of the masonry joints to such numbers:
- fireclay - 2 mm,
- furnace refractory - 4 mm.
Such parameters provide minimal shrinkage of the finished thermal unit. Also, thanks to thin seams, the masonry does not collapse during strong heating. For comparison: a seam 10 mm thick shrinks by 1 mm. Minimum joint thickness is especially important in the following places:

Modern technologies have made it possible to replace the masonry mortar with special adhesive mastics that can withstand temperatures up to 1300ºC. They are made from natural minerals, therefore they are environmentally friendly, have no odors when heated, and are resistant to alkalis and acids. Masonry is carried out by applying a layer of mastic with a thickness of 1 mm, which further increases the quality of the stove itself (fireplace).
Benefits. Processing methods
Features of stove bricks: they accumulate heat and evenly radiate it into the room. This allows you to warm the house for a long time after the firebox attenuation. It is enough to fill the furnace once with firewood and burn them for 3 hours, so that the stove continues to give off heat for 14 hours. Cutting kiln bricks by hand is difficult, as it is very durable. In order to avoid errors and obtain the exact dimensions of the material, it is better to use a power tool: a circular saw, a cutting machine.